FDY Color Yarn is a high-tenacity filament yarn designed to be used in warp or weft fabric construction, made of polyester with various colours available including Yellow, Black, Dope Dyed etc. Often seen used in apparel fabrics for industrial textile use and hometextile fabrics with benefits including high tenacity, good elasticity and reduced shrinkage.
Knitting or weaving this fabric with any filament yarn produces different varieties of fabrics for home furnishing, fashion, denim fabric production and Terry Towel production. Furthermore, the material can be further textured, dyed or sized according to customer need.
Fully drawn yarn differs from partially oriented (POY) in that it does not require texturing prior to being used for fabric creation, as its draw is completed during spinning itself and results in higher stability and better quality fabric than its POY counterpart.
FDY yarn can also be twisted at lower temperatures than POY yarn, saving energy and money for manufacturers while decreasing chances of warp/weft breakage and lengthening machine lifespan. Furthermore, its high resistance to oil/chemical exposure makes it perfect for heavy duty applications.
FDY yarn production is a complex process involving many steps and machines, which must be monitored closely to avoid defects like loop formation. Loops may negatively impact final products as well as cause issues during looming processes; to prevent this issue from recurring manufacturers must establish rigorous inspection rules and comply with quality standards for yarn.
While manufacturing FDY yarn, it is crucial to take special note of its sizing and finishing processes. As these steps can cause friction on filaments that creates loops in yarn, proper methods should be implemented within manufacturing facilities for their proper usage in this regard.
FDY yarn production requires careful consideration when it comes to temperature of the melt pool during extrusion. For best results, temperatures must remain comfortable to avoid looping. In addition, sizing should occur at a steady speed to avoid heat loss or uneven melting.
Last, it is essential to reduce contaminants in the melt pool by using appropriate raw materials and adhering to strict quality standards. Furthermore, manufacturing companies should monitor production closely to ensure it meets specifications for an end product of superior quality. Furthermore, production teams should be trained on how to identify defects quickly and take corrective measures for timely completion of FDY yarn manufacturing projects. With proper oversight in place and by taking these preventive steps successfully crafted yarn can be produced without loops!
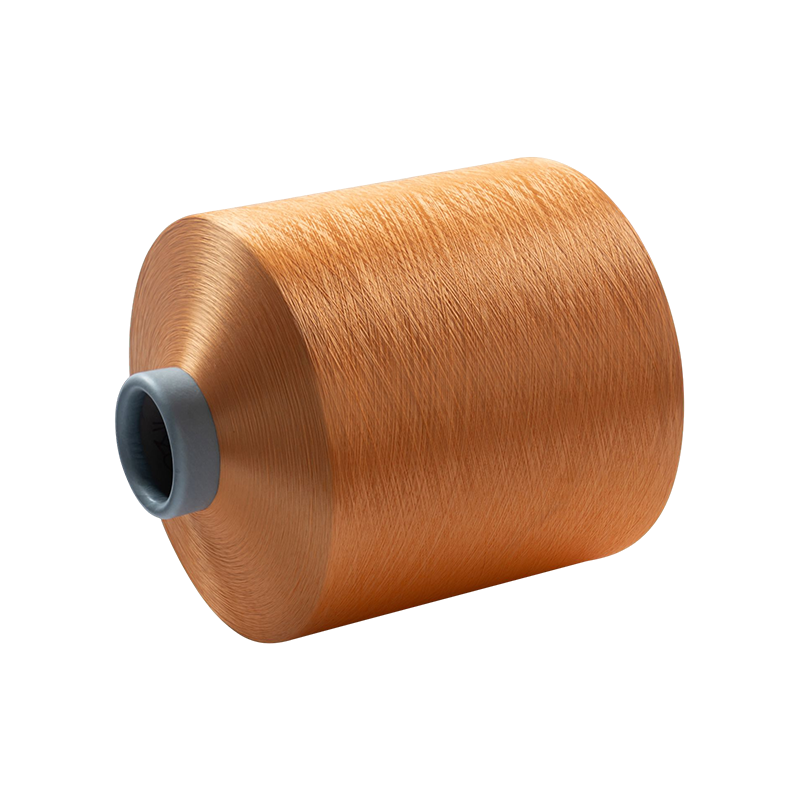